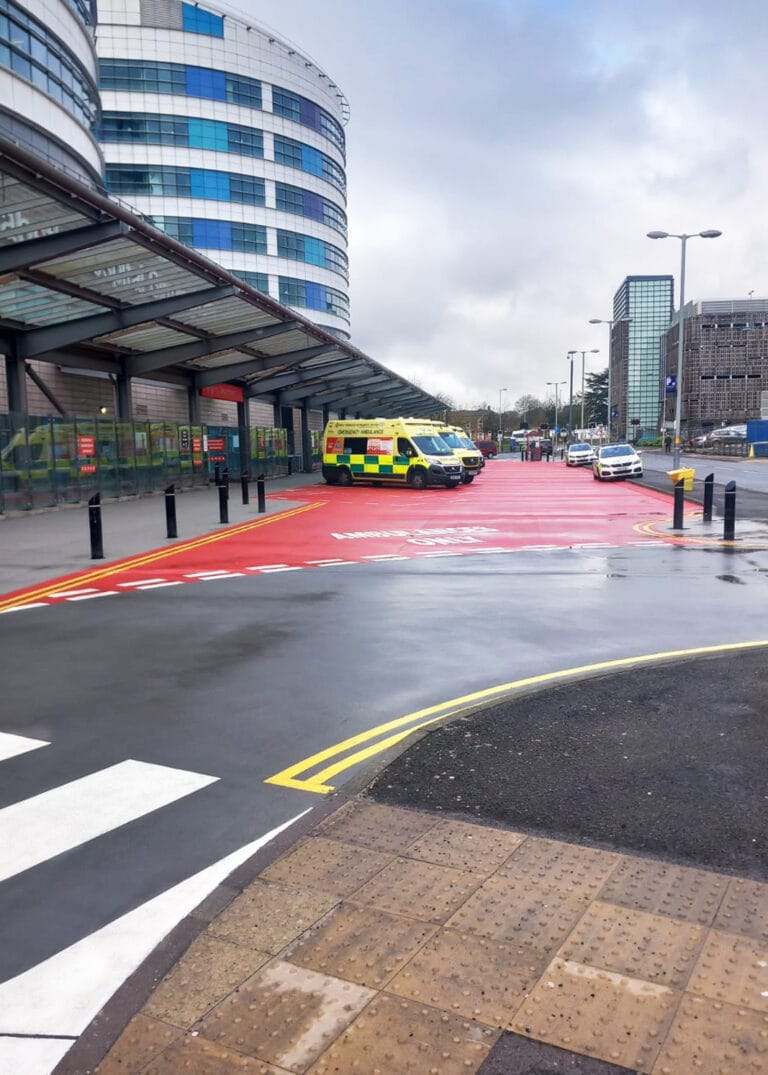
Client: Balfour Beatty
Role: Specialist Contractor
Scope
- Removal of Deck Coatings
- Concrete Repairs
Replacement Drainage
Replacement Joints - Deck Waterproofing
- Noise & Dust Control
Details
-
- Hospital A&E apron area
Removal and placement of Sika RB28 deck waterproofing system
Concrete repairs and rectification of spalling - Installation of a new drainage system and joints
8 phases to ensure ongoing hospital services with minimal disruption - Dust/odour control, waste management and sustainability prioritised
- Hospital A&E apron area
The Queen Elizabeth Hospital embarked on a complex refurbishment project with it’s Accident & Emergency area. This critical project involved a wide range of specialist works aimed at enhancing the structural integrity and functionality of the apron area.
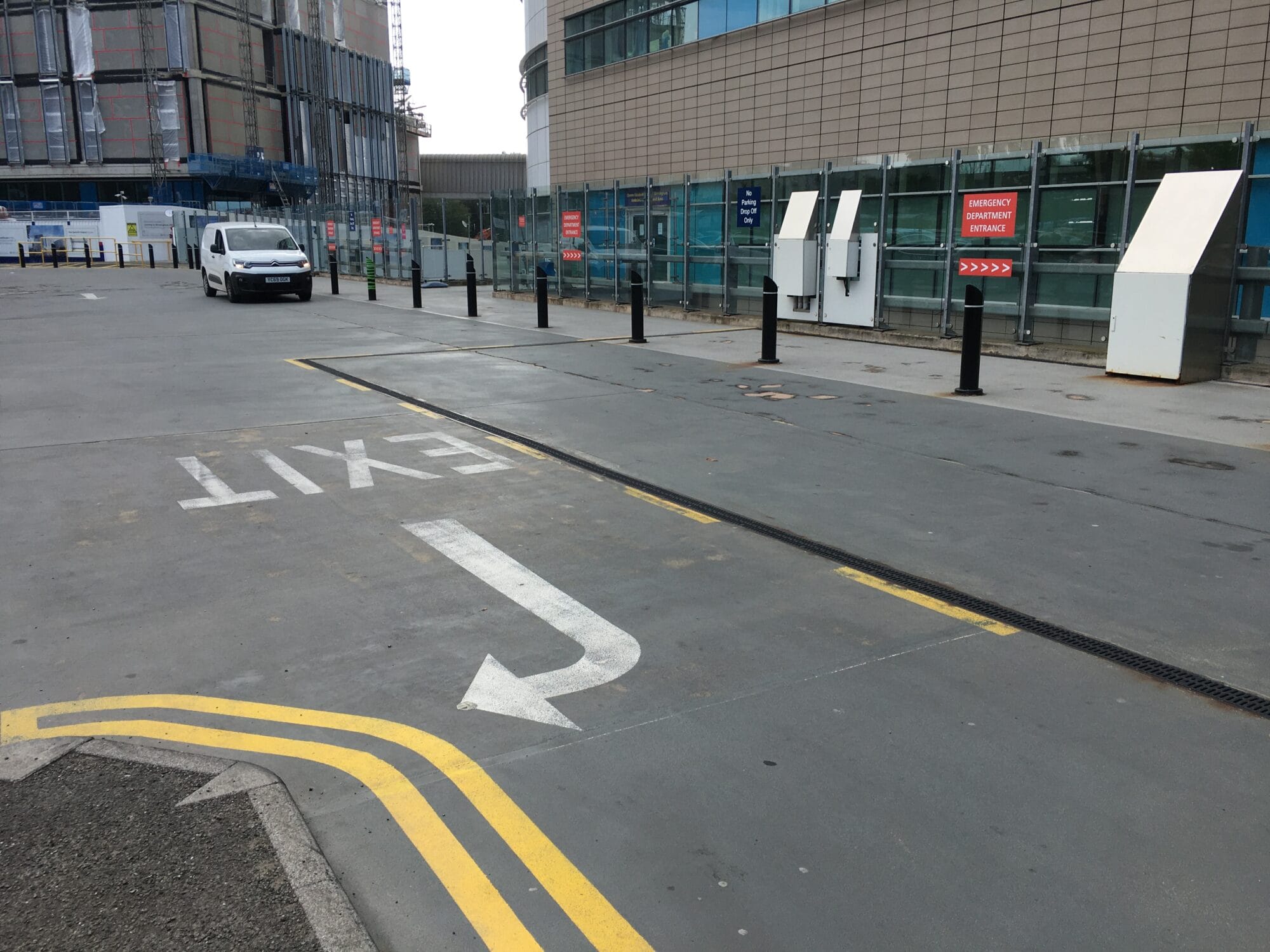
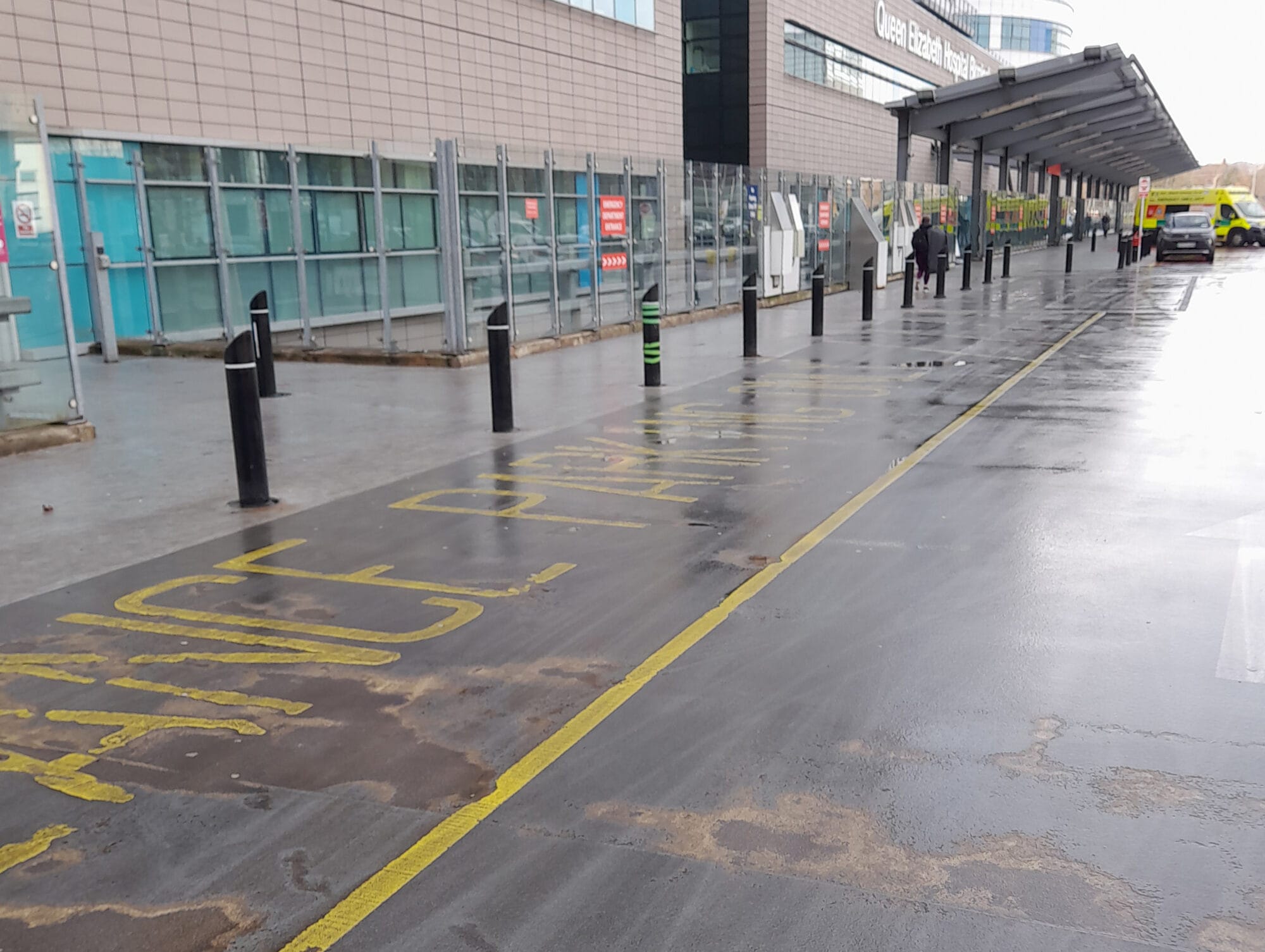
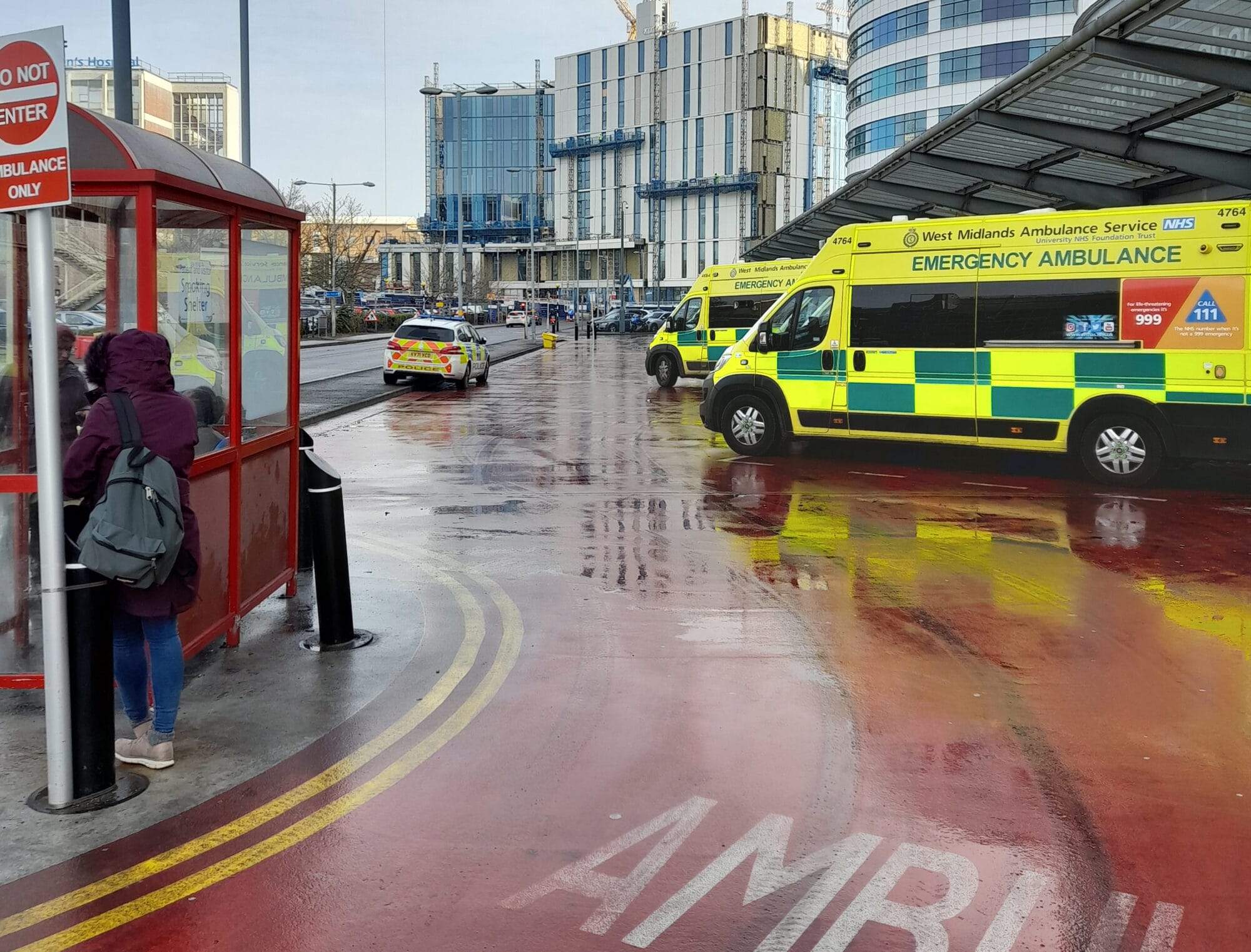
The key tasks included; the removal and replacement of the deck waterproofing systems, exposed concrete repair, rectification of spalling, installation of a new drainage system and the installation of new joints. Due to the high traffic nature of the hospital, minimising disruption to ongoing operations was paramount. As a result, the project was carefully separated into eight phase, ensuring continuity of hospital services while allowing the essential works to progress.
The initial stages of the refurbishment required the removal of the existing coatings, a task accomplished with the use of ride-on-planing machines. These machines ensured that the surface was adequately prepared for further work. A thorough assessment of the concrete was using hammer testing, which identified areas requiring repair. Pull-off tests were carried out to determine the substrate’s suitability for the application of the new deck waterproofing system. Edge preparation was also carefully executed to facilitate optimal adhesion of the Sika RB28 resin, a vital component of the waterproofing solution used.
Mitigating dust and noise was a critical concern due to the hospitals operational environment. Throughout the duration of the project, specialised measures were implemented to control these factors. Dust extraction systems were employed and noise barriers were strategically placed to limit the impact of the construction on both patients and staff. Regular environmental assessments were conducted to monitor acceptable levels of dust and noise.
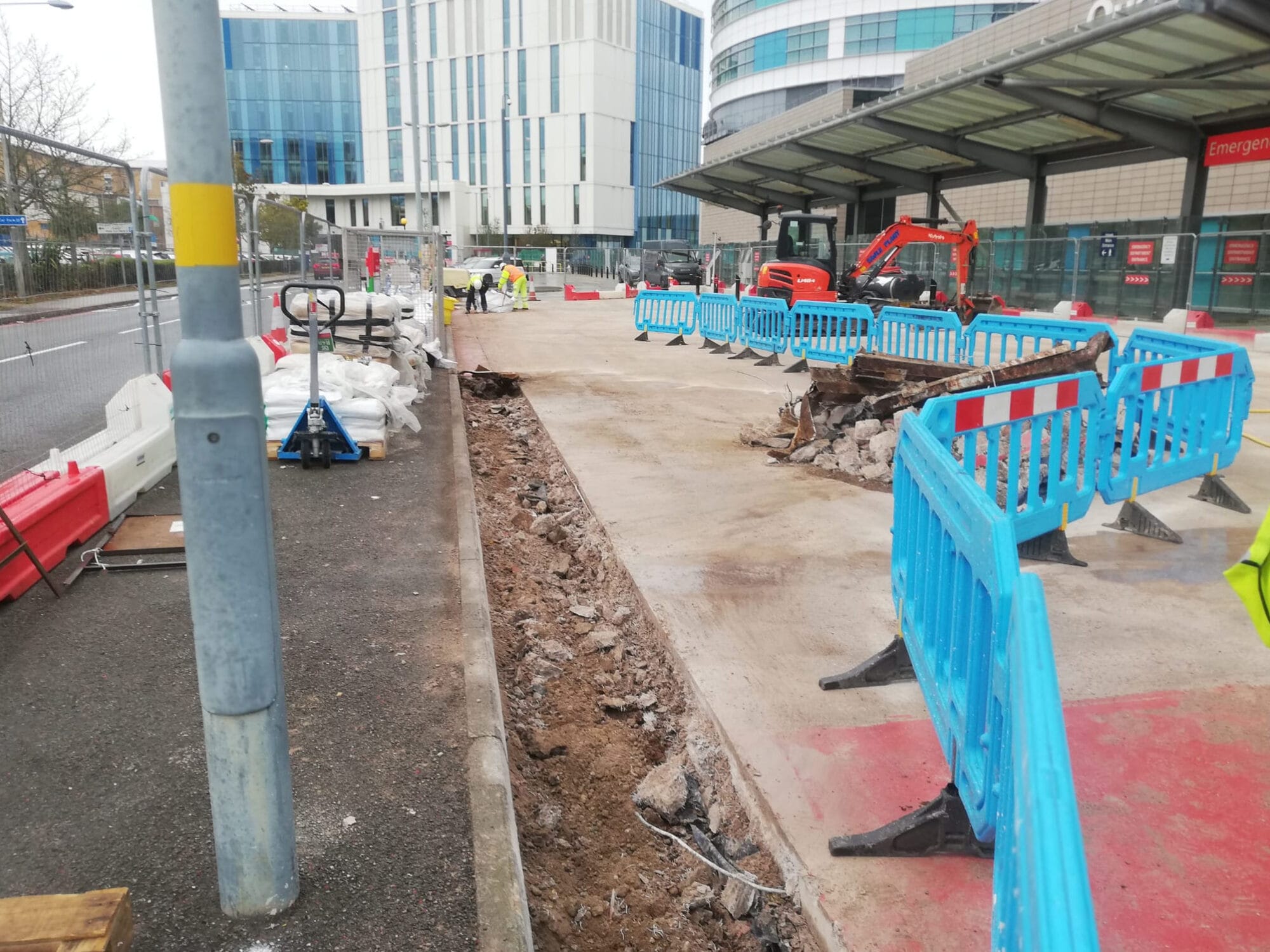
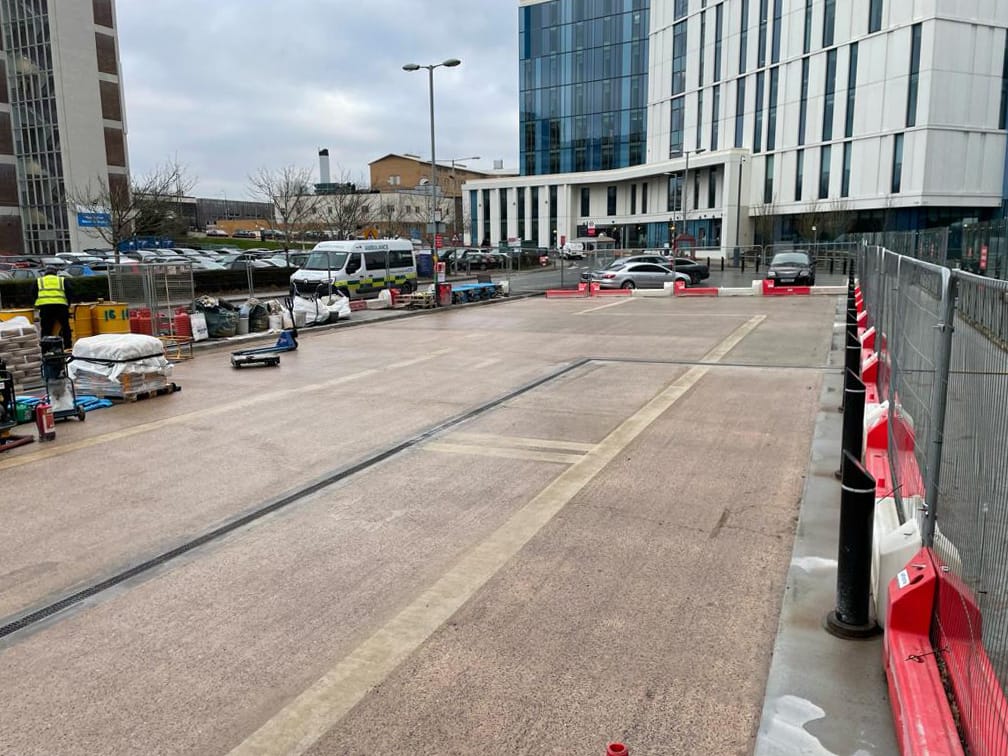
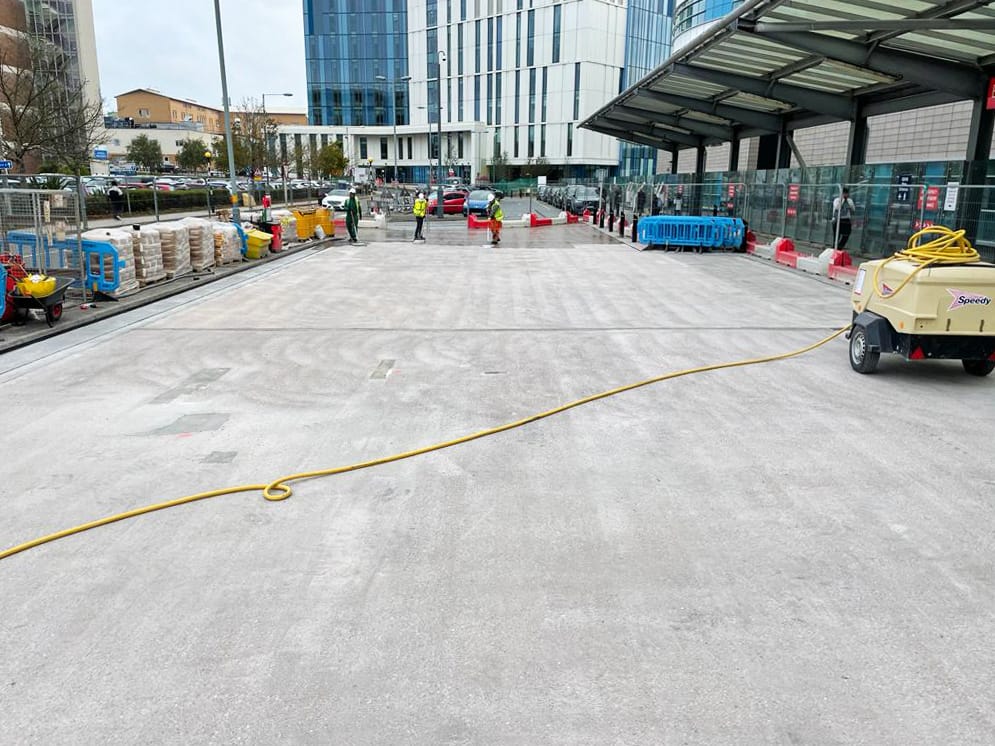
Health & safety were key priorities at every stage of the refurbishment. The project team ensured strict adherence to COSHH requirements and conducted ongoing inspections of substrate conditions, temperature, humidity and dew points. A permanent, qualified banksman was on-site throughout the works and to oversee the safe management of materials and personnel. Additionally, a specialist traffic management company was engaged to establish and maintain safe routes for both vehicles and pedestrians during each phase, ensuring minimal disruption to hospital operations.
Environmental considerations were also embedded within the project. Measures were taken to minimise dust emissions and control temporary odours that arose from the application of resin materials. Waste management was handled responsibly, with excess materials being transported away from site for appropriate disposal. Throughout the works, sustainability and environmental care was prioritised alongside the technical and operational requirements.
Thanks to the detailed planning, precision in execution and a firm commitment to health and safety, the refurbishment of the A&E apron at Queen Elizabeth Hospital was completed successfully. The works not only met the technical requirements but also preserved the functionality of the hospital throughout, ensuring that patient care was never compromised.
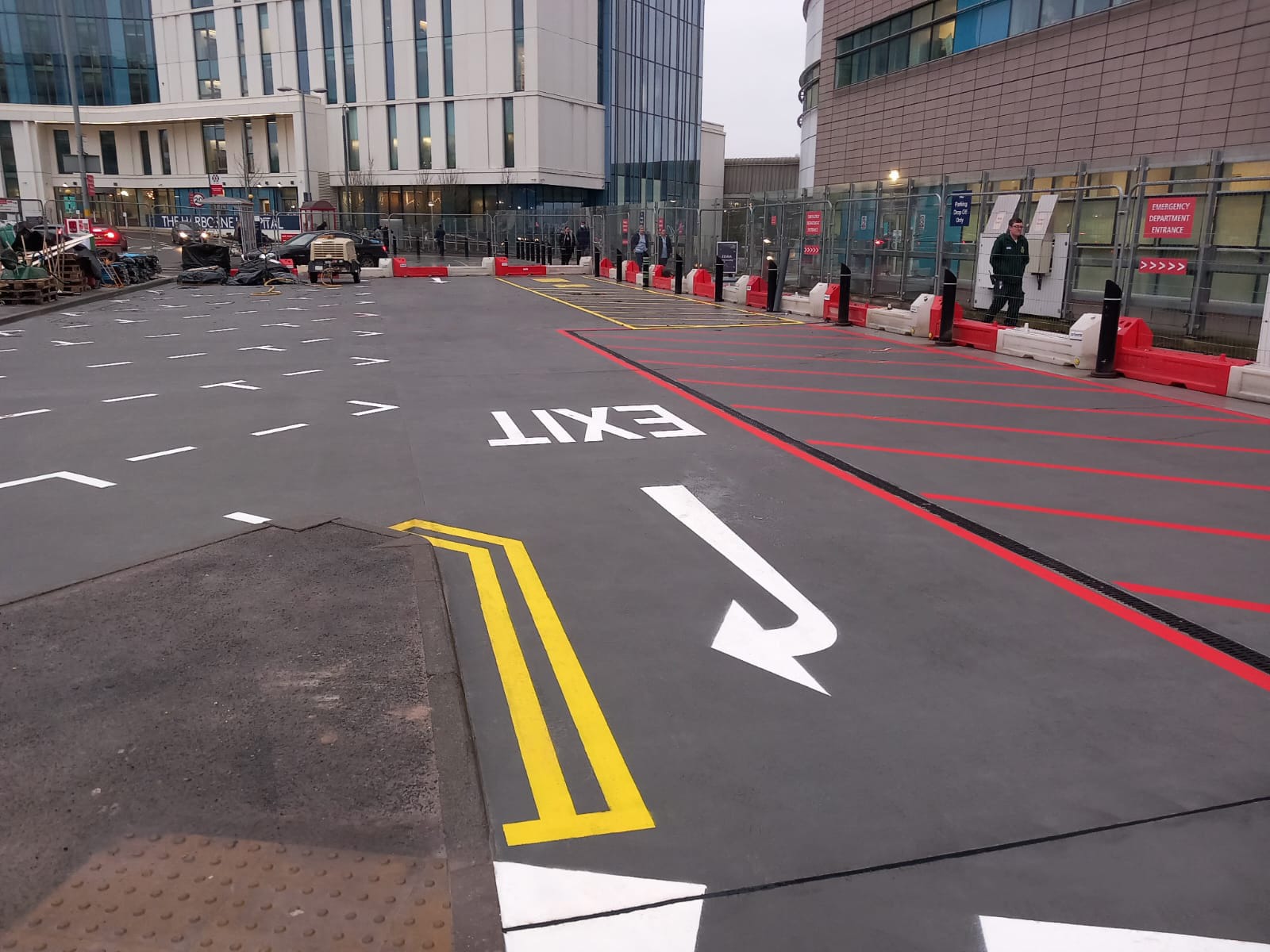
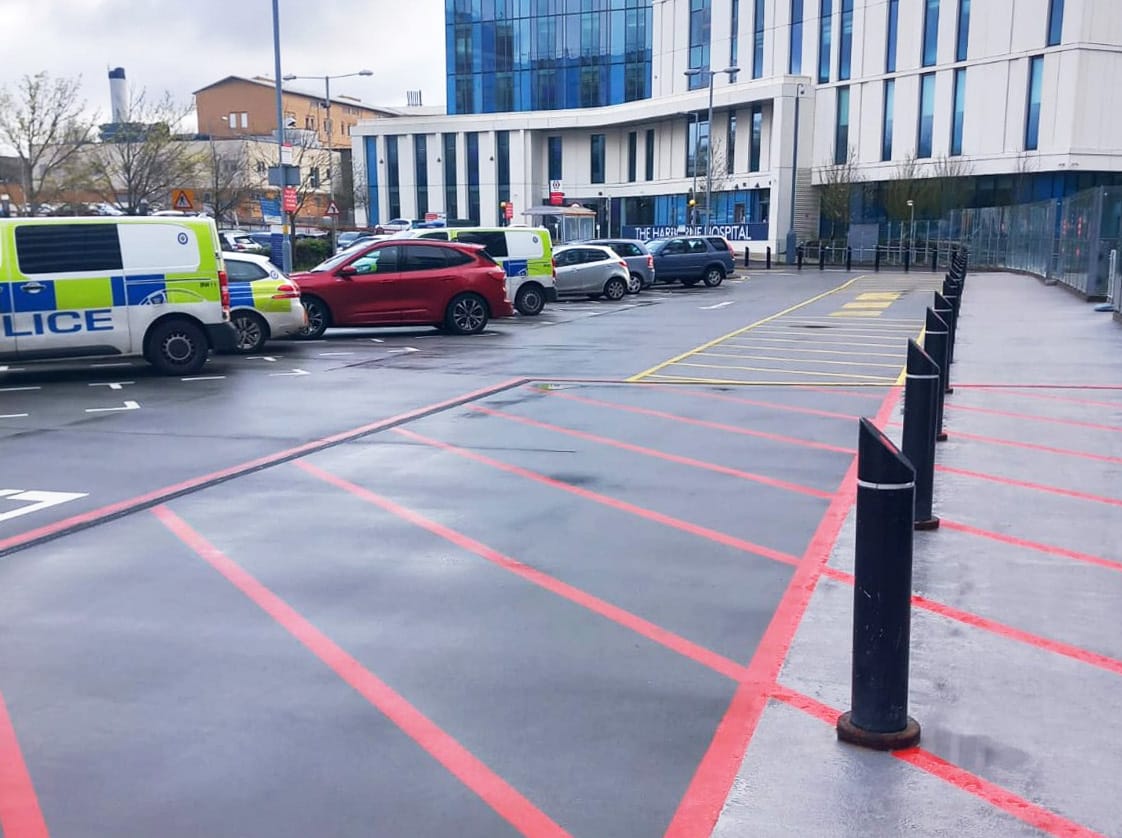
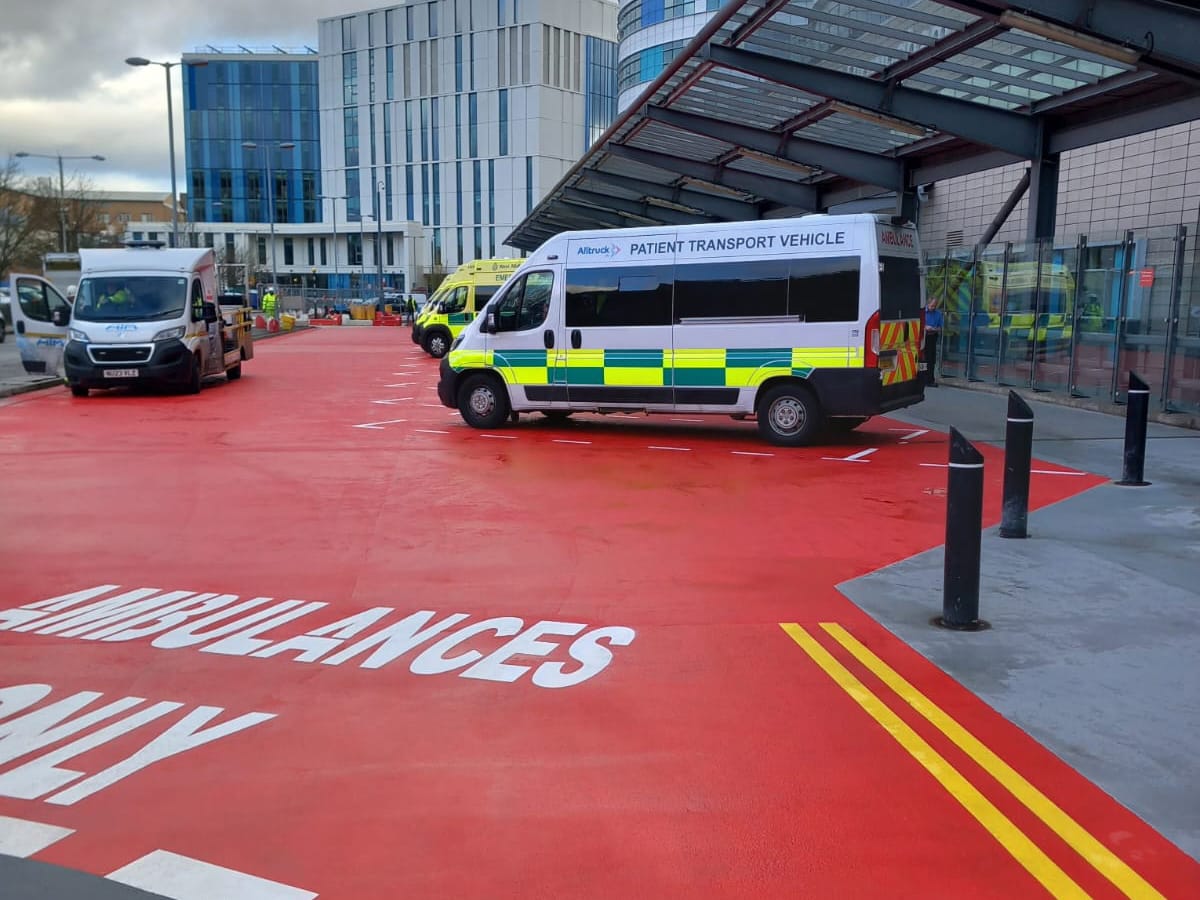