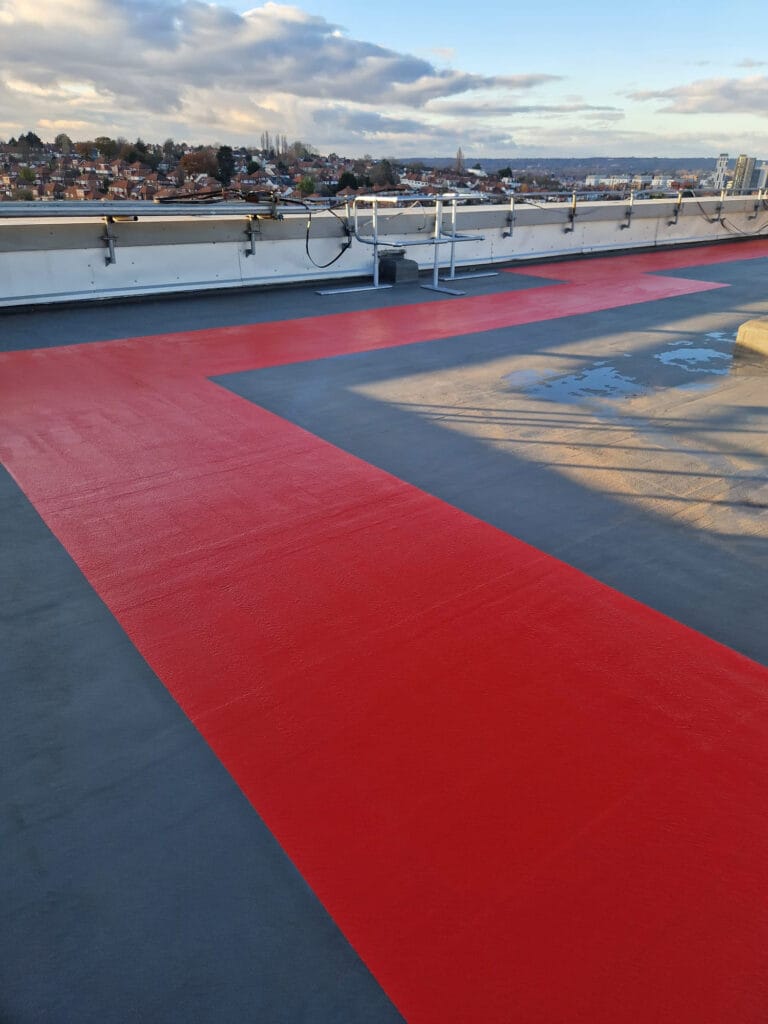
Client: MBRG Consulting
Role: Principal Contractor
Scope
- Asphalt Repairs
- Tapered Insulation
- Vapour Control Layer
- Roof Re-Waterproofing
- Anti-Slip Walkways
Details
-
- Hotel, office and residential building roof
- Localised replacement of insulation
Three roof decks comprising of 650m2 re-waterproofed
Anti-slip walkways
Hyde House is a notable building located in Hendon, a suburban area situated about 8 miles from Central London. This 12-storey structure serves as a Premier Inn hotel, catering to guests with its 108 rooms, making it a significant accommodation option within the region. The buildings multi-functional design includes offices on the top floor, illustrating its versatility in serving both business and leisure purposes. Additionally, a residential flat is located on the roof, occupied by the building’s caretaker, adds to the complex’s unique character.
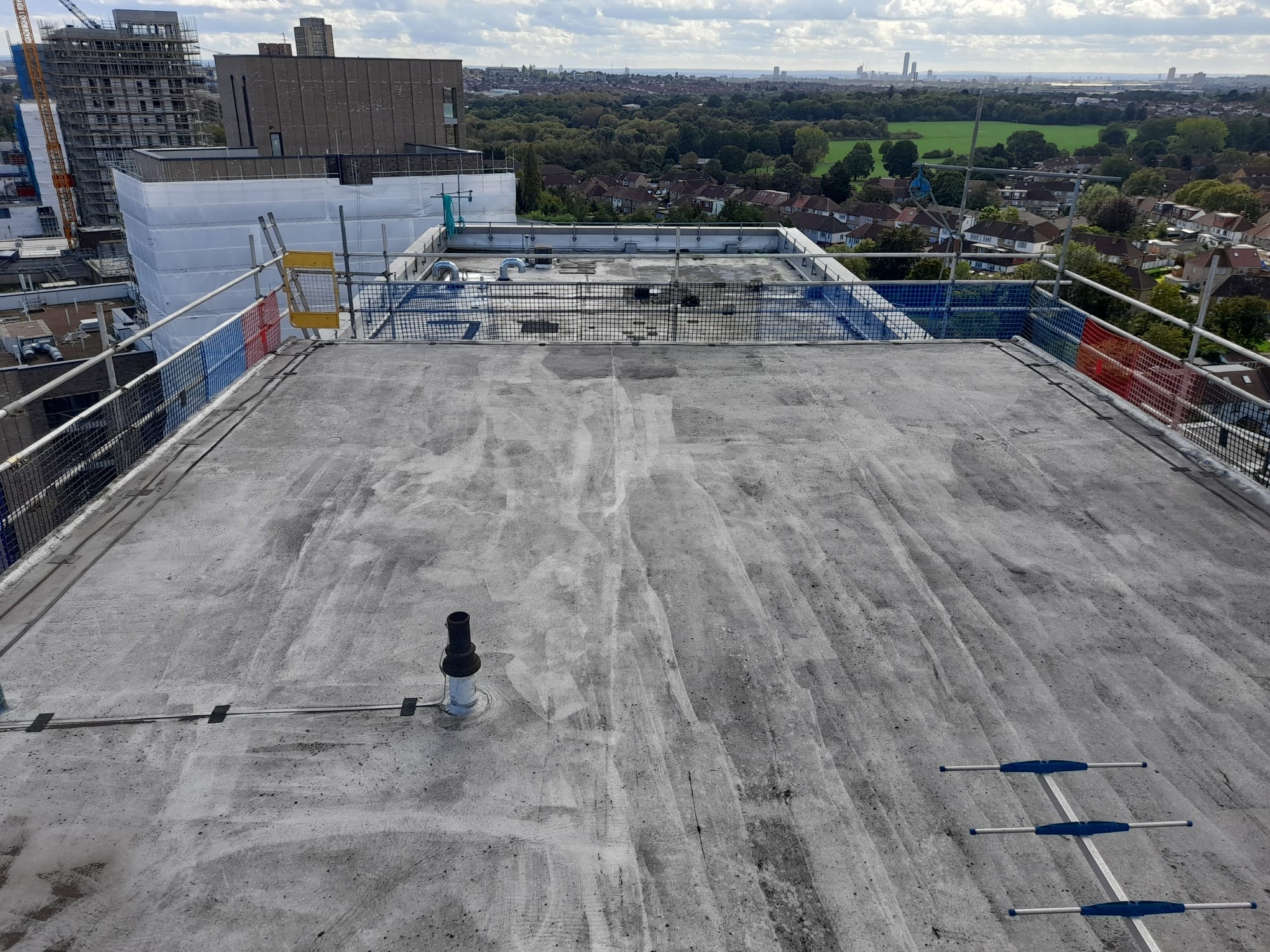
Before: Existing Aging Asphalt At The End Of Its Serviceable Life
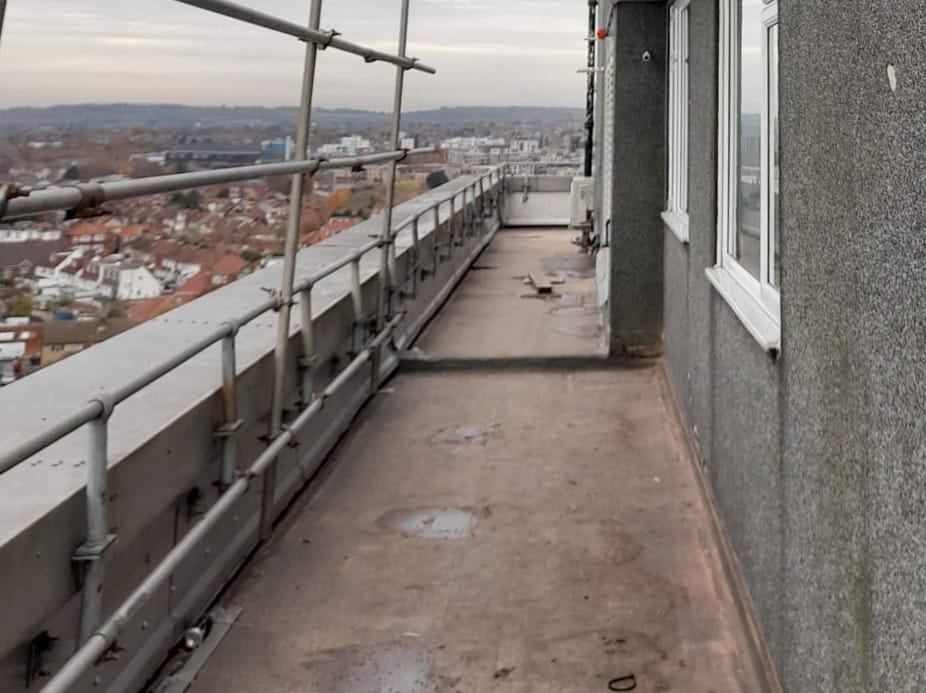
Before: Damaged Walkways
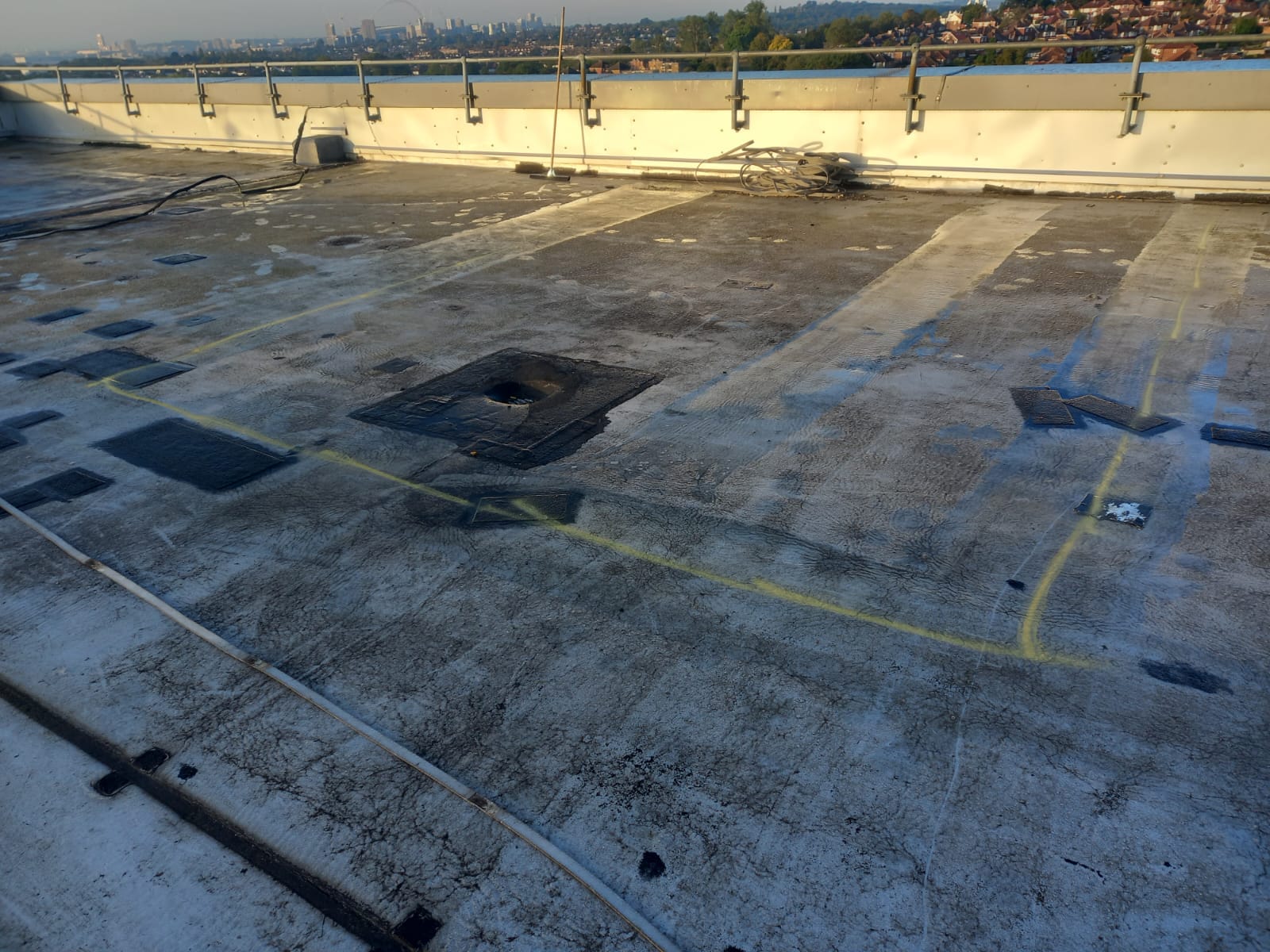
Before: Blistering & Cracked Waterproofing
The existing asphalt waterproofing system on the roof had come to the end of its serviceable life, causing water ingress in multiple locations, primarily due to cracks and blisters throughout the aging asphalt. In addition, there was an issue with ponding water in various areas of the roof, further compromising its integrity.
The refurbishment began with the removal of paving stones from around the residential property and addressing the damaged asphalt underneath. There was a substantial amount of cracks throughout the entire roof, whilst blisters were mainly near the paving stones. These were repaired using a heat lance before the substrate was power washed to remove any vegetation and/or debris to ensure a clean and suitable surface for the new system.
One specific area on the main roof, near the drainage outlets, required more intrusive repairs. The asphalt in this section was stripped back and the underlying insulation, which had been compromised by water ingress, was removed and replaced with 80mm PIR insulation. Once the new insulation was installed, the area was built back up and prepared for the new waterproofing system.
Following the preparation of the substrate, a primer layer was applied to enhance the adhesion of Westwood’s WeCryl R230. This primer acts as a bridge between the roof surface and the waterproofing membrane, promoting better adherence and performance. Once the primer was cured, the WeCryl R230 was meticulously applied, using rollers to ensure an even and consistent layer. The seamless application of the waterproofing system covered the entire roof surface and intricate detailing, including penetrations and upstands, which are common areas prone to leaks.
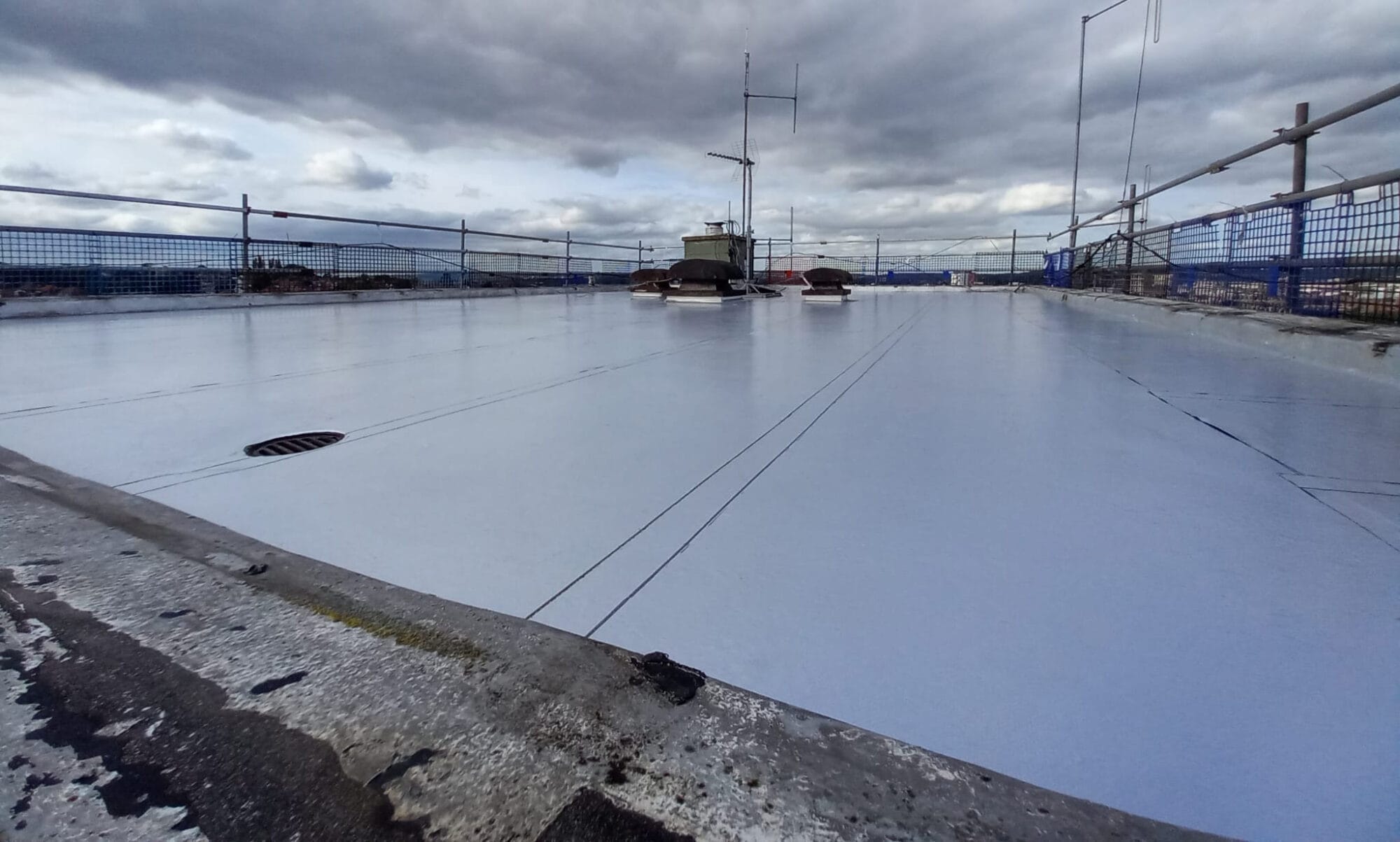
During: Installation Of Vapour Control Layer
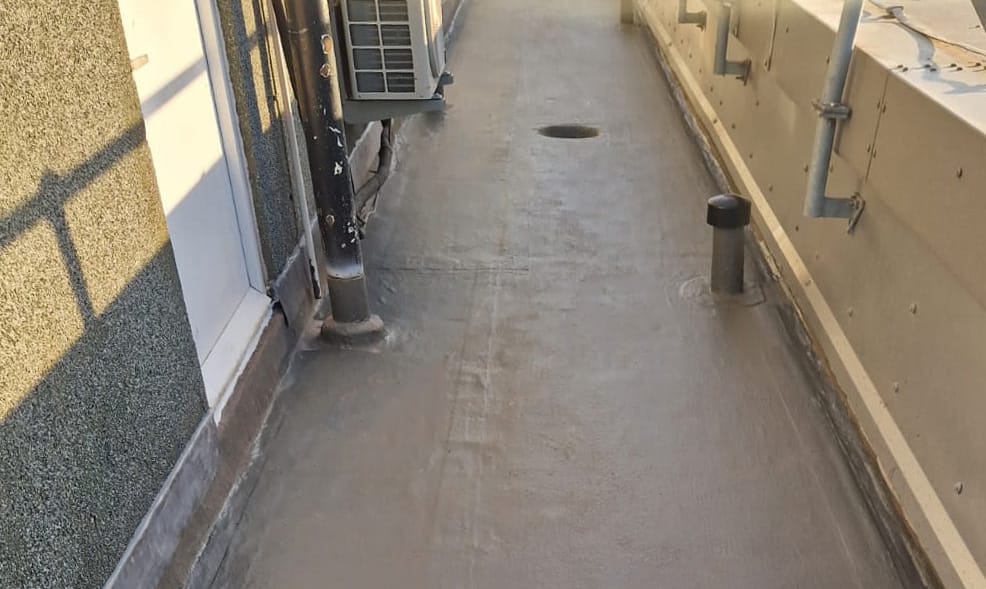
During: Walkway Waterproofed Ready For Anti-Slip Coating
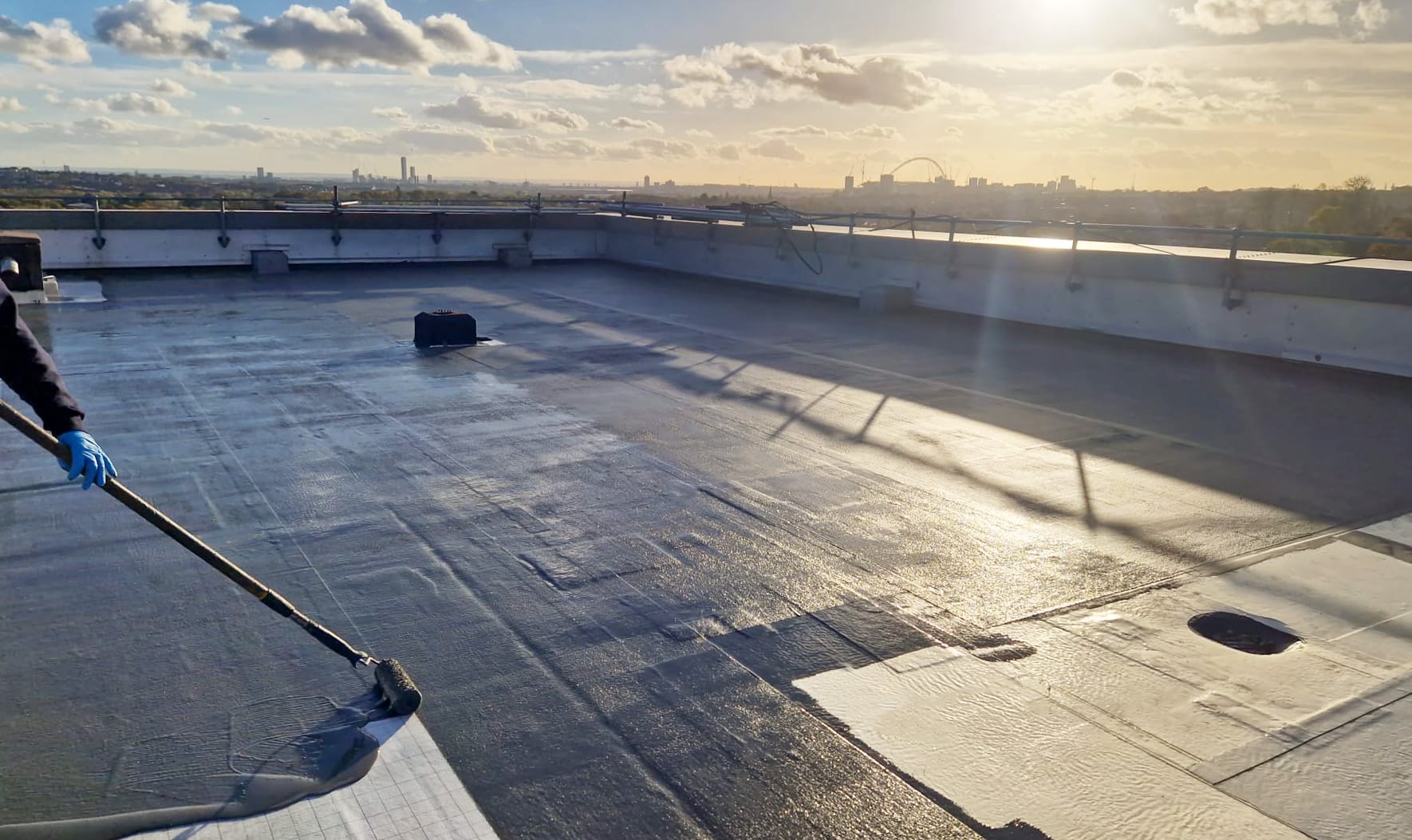
During: Application Of Waterproofing
Westwood’s WeCryl R230 was selected due to its exceptional properties that cater specifically to creating a seamless and durable waterproofing system. This product is known for its high elasticity, crack-bridging abilities and resistance to various weather conditions, which makes it ideal for structures where long-term durability is crucial.
Furthermore, the flexibility of the system allows it to accommodate structural movements and thermal expansion without compromising its integrity. This adaptability ensures that the waterproofing system remains intact and effective, even under varying temperatures and environmental conditions, meaning it was the ideal system to be used on this project.
An anti-slip maintenance walkway was overcoated around the perimeter of the building to improve safety for anyone accessing the exterior areas. Whilst the waterproofing system was being applied, high friction quartz sand was scattered evenly to prevent any slips, trips and falls in all weather conditions. New like for like paving slabs were also installed in front of the flat. These matched the original ones in design and appearance, maintaining the aesthetic continuity of the property while ensuring a fresh, even surface.
Additional works on-site include the installation of new fascia and soffit boards for the residential flat, as well as the replacement of guttering and downpipes. These enhancements were necessary to complement the new waterproofing system and ensure efficient drainage, further mitigating the risk of water damage.
The refurbishment project at Hyde House effectively addressed the critical issues of water ingress and ponding water. The application of Westwood’s waterproofing system, along with the additional and drainage improvements, ensured the roof’s integrity and extended its serviceable life. The project considerably enhanced the overall safety and functionality of the building, providing long term benefits for the hotel and its residents.
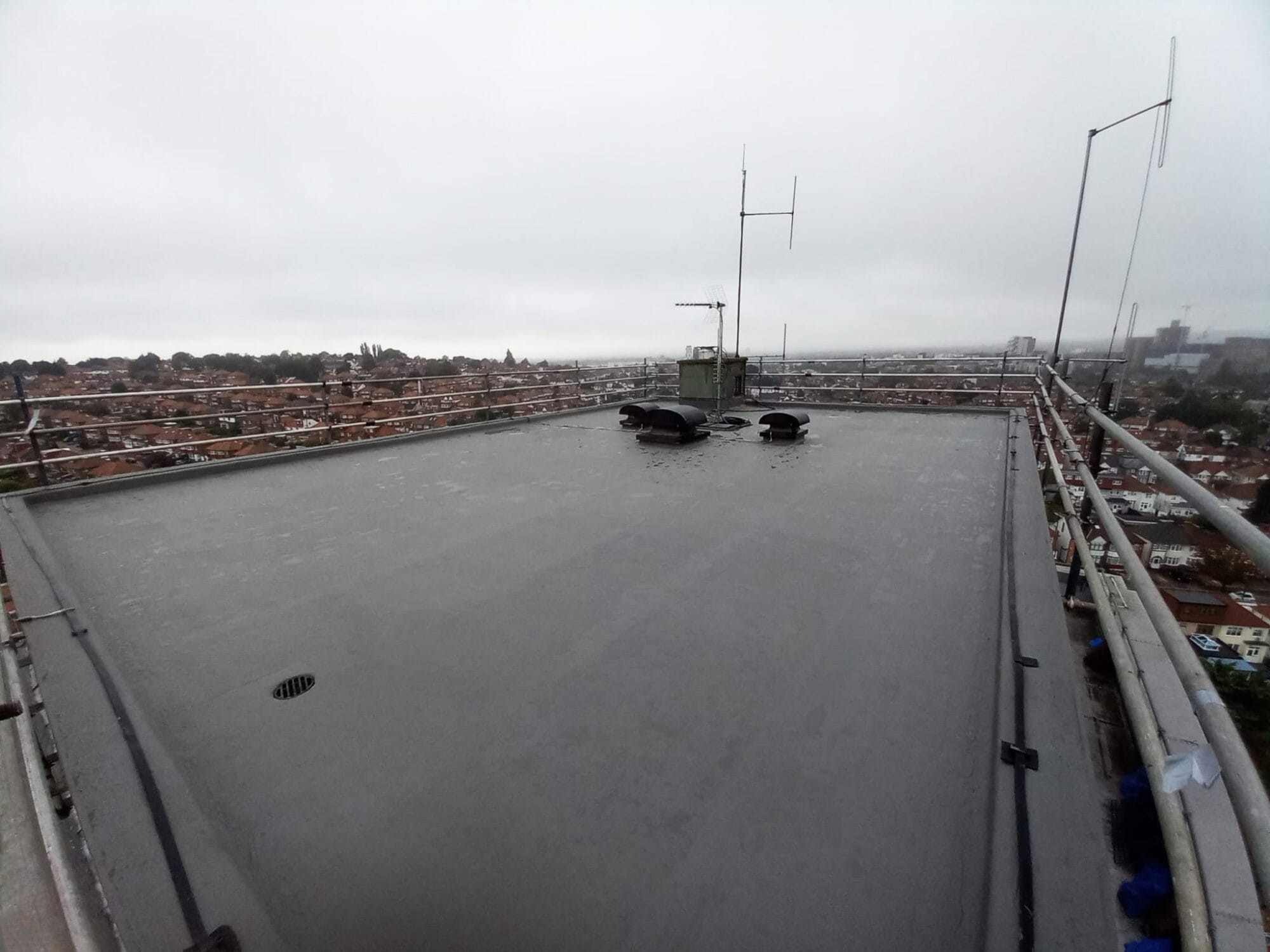
After: Seamless & Watertight Application
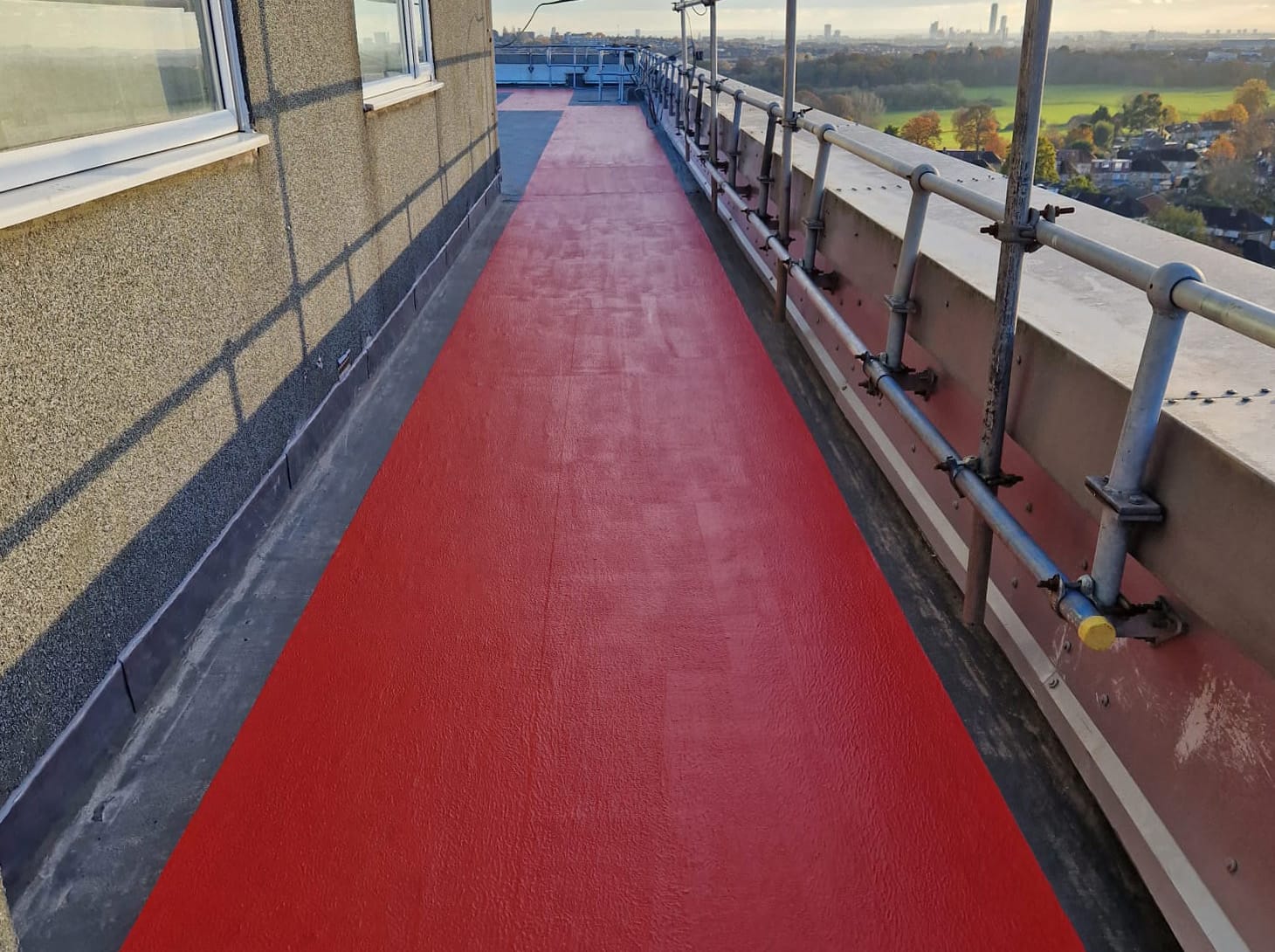
After: Anti-Slip Walkway For Employees Safety

After: Asphalt Repaired & Re-Waterproofed