Corrosion Management
The corrosion process of reinforcing steel with concrete presents a unique challenge. Conventional patch repairs, which focus only on visible defects, often introduce the ‘incipient anode’ effect. This occurs when a new, alkaline repair area is placed next to untreated, chloride-contaminated concrete, creating new corrosion potentials around the repaired area.
Since concrete repairs typically address only small portions of the structure, large areas remain untreated, which can lead to further corrosion. To mitigate this risk, it’s essential to implement a comprehensive corrosion management strategy as part of the repair and protection process.
Corrosion management is a crucial aspect of achieving a successful car park refurbishment. Client requirements vary, with some opting for short-term repair strategies due to budget constraints, while others seek longer-term solution. Understanding the causes of corrosion, such as the impact of de-icing salts and carbonation on reinforced concrete, is vital for planning an effect repair and protection strategy.
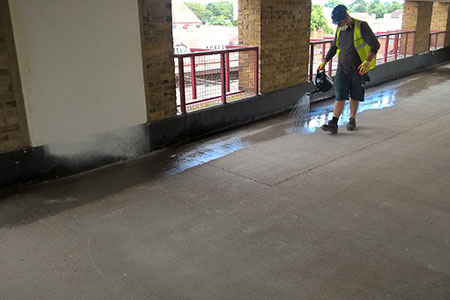
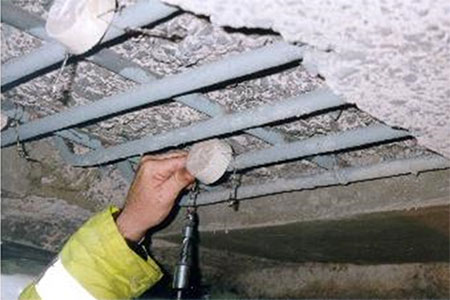
The effects of de-icing salts and carbonation on reinforced concrete can vary in severity, making it essential to understand the causes of corrosion when planning a car park’s repair and protection strategy. Corrosion occurs through a complex interaction of factors including, water, oxygen and chloride salts, which, when combined, can initiate and accelerate deterioration.
Corrosion management techniques include:
Multi-functional Corrosion Inhibitors (MCI’S)
Vapour-phase Corrosion Inhibitors (VCI’s)
Sacrificial Galvanic Anodes (Embedded)
Impressed Current Cathodic Protection